QC検定3級のおすすめテキスト『ゼロからわかる! QC検定® 3級 テキスト & 問題集 新装版 [最新レベル表対応](TAC出版)』を用いて出題内容を本記事にまとめ上げましたのでご覧ください。
QC検定4級のまとめ記事の内容からスムーズに接続できる内容となっております。
Amazonのレビューなどでも本書のインプットとしての使いやすさ、そして巻末模試の良さなどがあり、本書のみでも合格には問題ないと考えます。しかし更なる上位級を目指す方には、公式が出している過去問集『過去問題で学ぶQC検定3級 2025年版』を併用した学習をおすすめします。僕も1冊のみ購入し数回分の過去問演習を行い、2025年3月の第39回の試験で合格ラインを超えることができました。
品質の種類
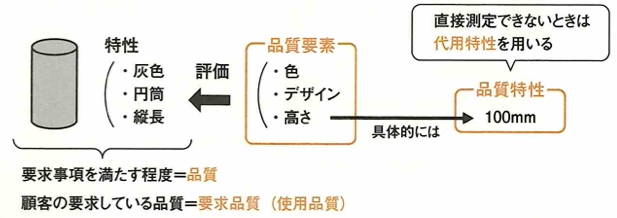
品質とは本来備わっている特性の集まりが要求項目を満たす程度と定義されています。
品質要素とは製品を評価する項目です。
要求品質(使用品質)とは顧客の要求している品質のことで、特性を直接測れない時は代用特性を用います。
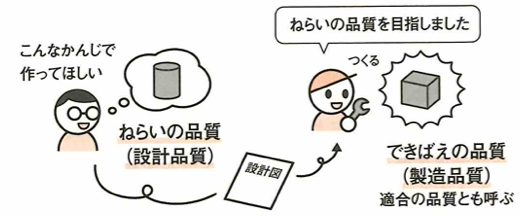
ねらいの品質(設計品質)を目指し作られたものをできばえの品質(製造品質)→顧客満足(CS)を高めます。
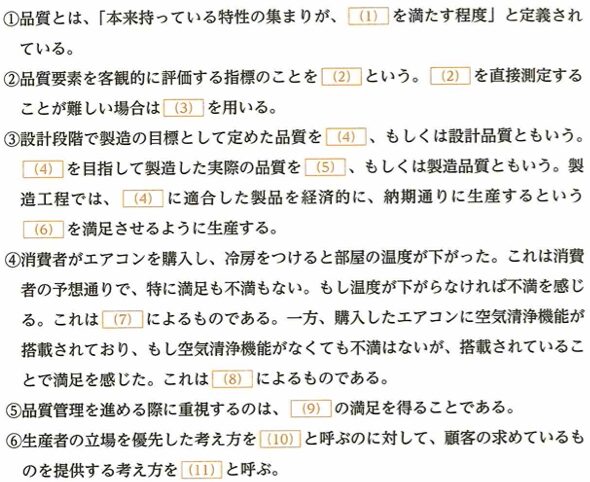
順に、要求事項、品質特性、代用特性、ねらいの品質、できばえの品質、QCD、当たり前品質、魅力的品質、顧客、プロダクトアウト、マーケットインです。
社会的品質を設けて迷惑の程度の低下を目指します。

プロセス⊃工程の考え方が大事です。また4M+measurement=5Mといいます。工程解析を行うことが大事です。
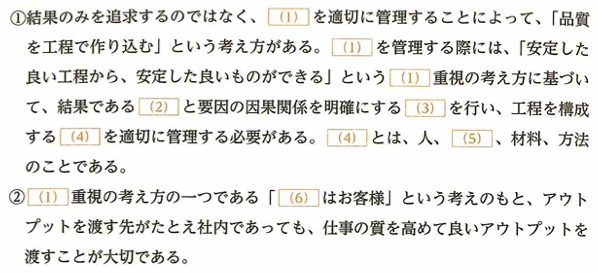
順に、プロセス、特性、工程解析、4M、機械、後工程です。
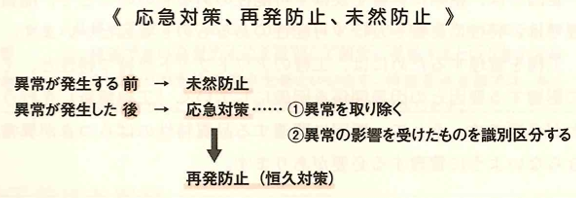
未然防止(異常発生前)→DR(デザインレビュー)FTA(fault tree analysis)FMEA(failure mode and effects analysis)
応急対策(異常発生後)→異常を取り除き、識別区別する。
再発防止(恒久対策)や水平展開(類似の工程がないか探す)
FTAは論理記号を用います。
工程管理では5Mや5SやQCD+PSME(品質、コスト、納期+生産性、従業員の安全、心の健康、地球環境)を総合的に捉えます。
問題が起きないように上流(源流)のプロセスを管理(源流管理)したいですね。
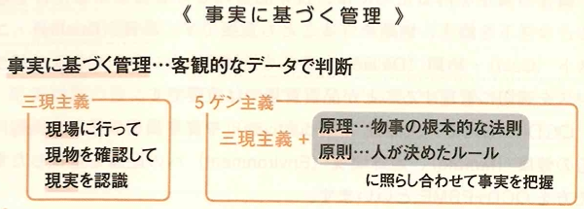
従業員満足(ES)も意識したいところですね。
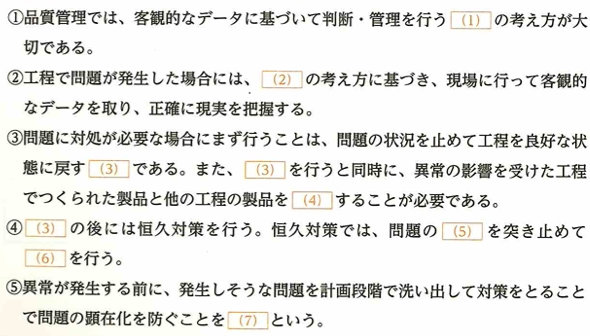
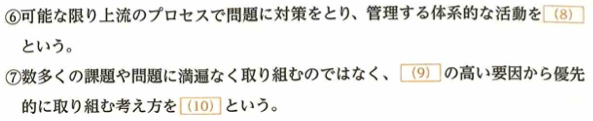
順に、事実に基づく管理、三現主義、応急対策、識別区分、根本原因、再発防止、未然防止、源流管理、寄与率、重点指向です。
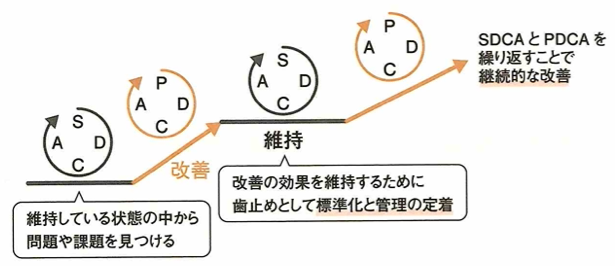
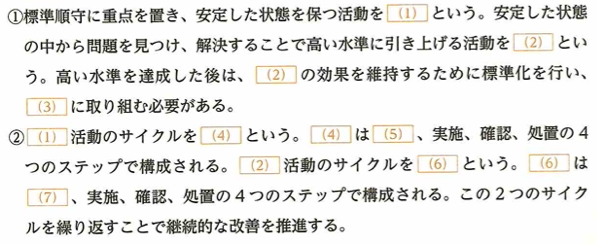
順に、維持、改善、歯止めと管理の定着、SDCA、標準化、PDCA、計画です。
問題は克服するもので課題は達成するものです。
問題は設定した目標と現実とのギャップです。課題は設定しようとする目標と現実とのギャップです。
課題達成型QCストーリーと問題解決型QCストーリー(8つの手順)は異なります!計画立案にはガントチャート(計画などを棒線で表し時間経過を見える形にしたグラフ)も用います。
手順1:テーマの選定
手順2:現状の把握と目標の設定
手順3:要因の解析
手順4:対策の立案
手順5:対策の実施
手順6:効果の確認
手順7:標準化と管理の定着
手順8:反省と今後の対応
語呂合わせですが問題解決型の方の8つの手順はテ現要対対対標反で覚えます。
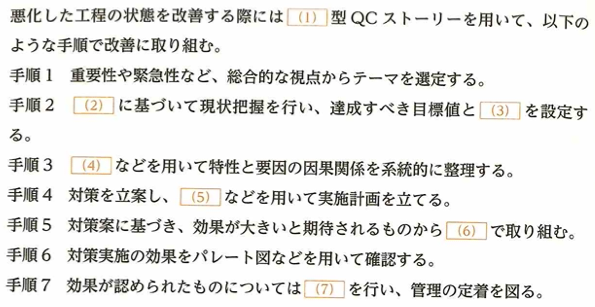
順に、問題解決、三現主義、達成期限、特性要因図、ガントチャート、重点指向、標準化です。
課題達成型のQCストーリーは9つの手順があります。
手順1:テーマの選定
手順2:QCストーリーの選定
手順3:攻め所と目標の設定
手順4:方策の立案
手順5:成功シナリオの追求
手順6:成功シナリオの実施
手順7:効果の確認
手順8:標準化と管理の定着
手順9:反省と今後の対応
課題達成型の方の9つの手順はテQ攻方成成効標反で覚えます。
どちらも初めはテで最後は標反ですね笑。また上は対が3つで下は成が2つですね。
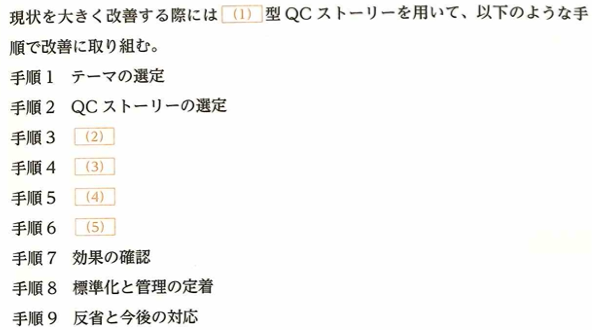
順に、課題達成、攻め所と目標の設定、方策の立案、成功シナリオの追求、成功シナリオの実施です。
品質保証
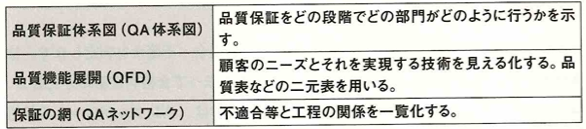
結果の保証よりもプロセスの保証が大事です。ライフサイクルアセスメントを意識します。そのため品質保証体系図を意識します。品質機能展開(QFD)で設計の意図を製造工程まで展開することを目的にします。そこで品質表などを用いて見える化します。
保証の網(QAネットワーク)つまり不適合等と工程を一覧化した表を用いて異常発生を防止します。
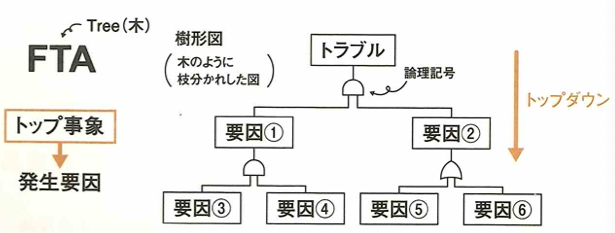
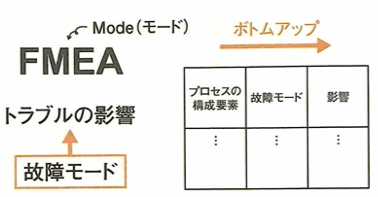
企業はPS(製品安全)やPL(製造物責任)と共に製品を製造して行きます。
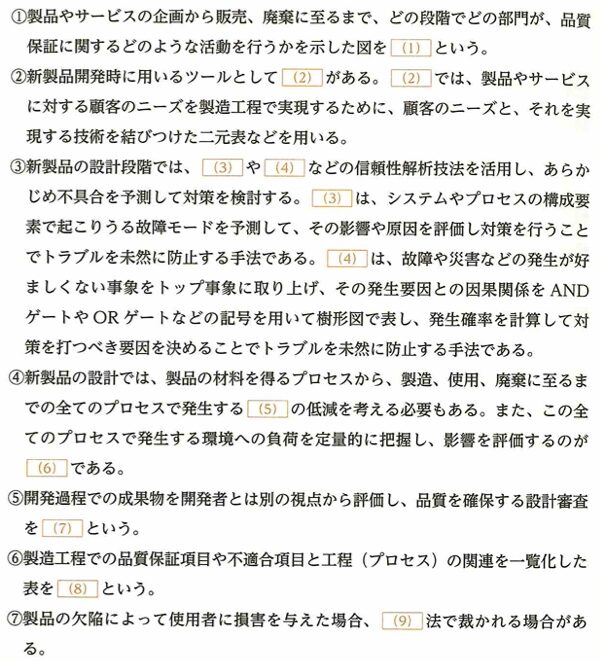
順に、品質保証体系図、品質機能展開、FMEA、FTA、ライフサイクルコスト、ライフサイクルアセスメント、DR、保証の網、PLです。
QC工程図とはプロセスの流れをフローチャートで表した文書で、管理項目や管理水準、管理方法などを記載します。工程解析と工程能力調査を行い、ばらつきについて調査します。
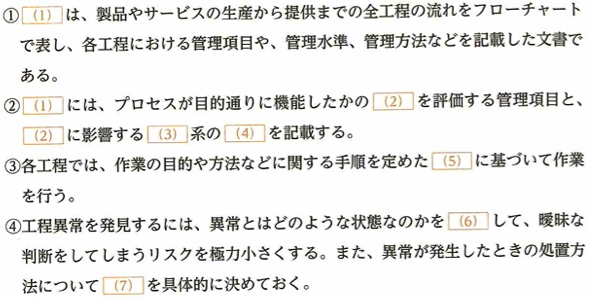
順に、QC工程図、結果、要因、点検項目、作業標準書、定義、5W1Hです。
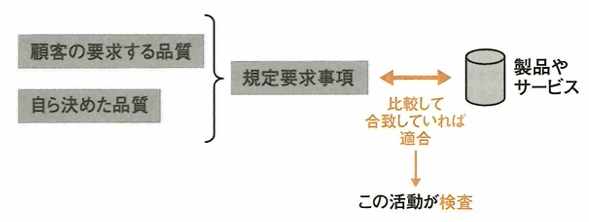
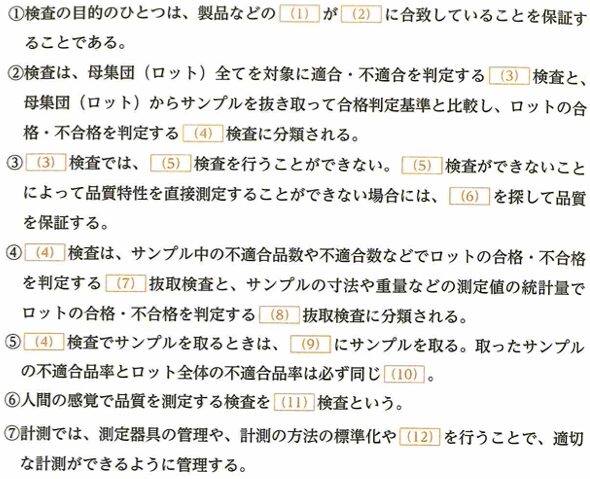
順に、特性値、規定要求水準、全数、抜取、破壊、規定要求事項、計数値、計量値、ランダム、になるとは限らない、官能、訓練です。
品質経営の要素
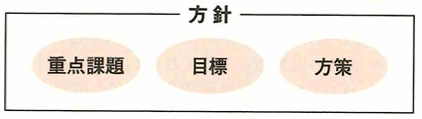
方針⊃重点課題+目標+方策
文章業務において、決められた標準類を遵守しながら効率的に行います。TQMとは組織全員が参加し品質の維持や向上を図る活動です。
標準化を行う目的は、相互理解の促進や互換性の確保や多様性の調整があります。わかりやすく文書化します。
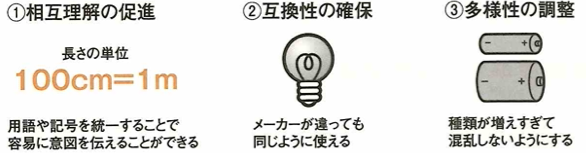
小集団活動→共通の目的を持った少人数チームで改善活動に取り組む方法です。
職場別グループと目的別グループに大別されます。
職場別グループ→QCサークルのようなボトムアップ型グループで活動を自主的に行う点が特徴です。
目的別グループ→プロジェクトチームのように企業関係なしのトップダウン型グループで終わったら解散します。

Off-JTとはoff the job trainingです。
ISO9001とは顧客のニーズに応えるためプロセスを改善し、顧客の信頼を得るために組織の活動に関する国際規格です。プロジェクトチームは経営資源を効率よく使うもキーワードです。
最後に確認問題を行います。
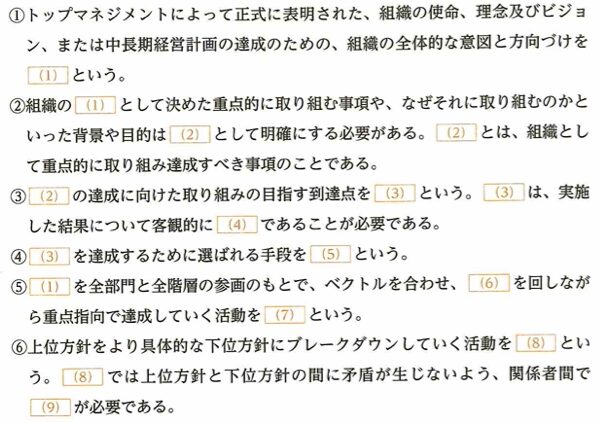
順に、方針、重点課題、目標、測定可能、方策、管理のサイクル、方針管理、方針展開、すり合わせです。
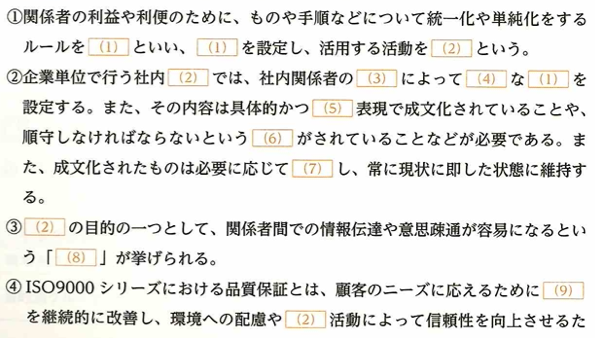

順に、標準、標準化、合意、実行可能、客観的、権威付け、改訂、相互理解の促進、プロセスです。
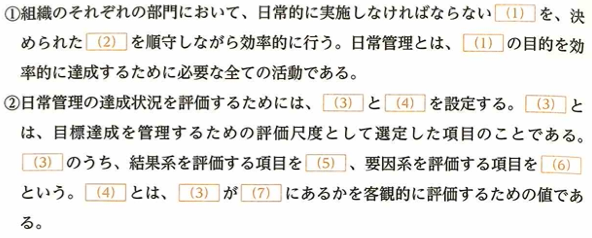
順に、分掌業務、標準類、管理項目、管理水準、管理点、点検点、安定状態です。
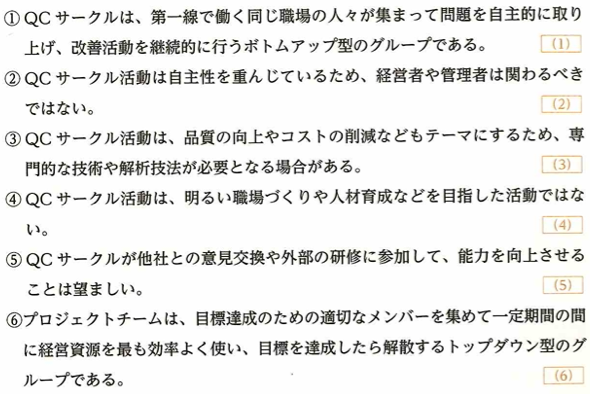
順に、◯×◯×◯◯です。
データの取り方とまとめ方
データ⊃数値データ(連続量の計量値と離散値の計数値)と言語データ
問題解決の手法は数値データはQC七つ道具で言語データは新QC七つ道具を用います。
サンプリング⊃ランダムサンプリングと有意サンプリング(夜に製造したものを選ぶなど)
かたよりとばらつきの違いを教えてください!
かたより→真の値と平均値の差
ばらつき→値の大きさが揃っていない度合い
誤差にはサンプリング誤差と測定誤差があります。
QC七つ道具とは数値データを解析して問題の解決を進める手法です
語呂は、樋口さんは突貫送別です。
層別
他のツールとともに用いる時もあります。
パレート図
縦軸にお金を持ってくる時もあります。
特性要因図
魚の骨に見立てたものです。これは工程解析の1つです。
ヒストグラム
一般型→ベル型です
→工程が安定しています。
二山型→ピークが左右に2つ→層別で対処します
→平均値の異なる二つの分布の混在。
離れ小島型→本体より少し離れた位置に小山があります
→工程異常、測定の誤り、他工程データの混在。
絶壁型→端が切れたもの→規格外のものを除いた場合です
→規格外れを除いたもの。
歯抜け型→区間の度数が交互に増減しています
→区間の決め方が不適切、測定のやり方の癖。
高原型→区間の度数にあまり差がないもの→層別で対処します
→複数分布の混在。
離れ小島型のときは工程異常、測定誤り、他の工程のデータが混じっているなどが考えられます。
歯抜け型のときは区間の決め方が不適切か測定のやり方に癖があるなどが考えられます。
離小島型が最も問題児みたいな扱いで面白いですね笑
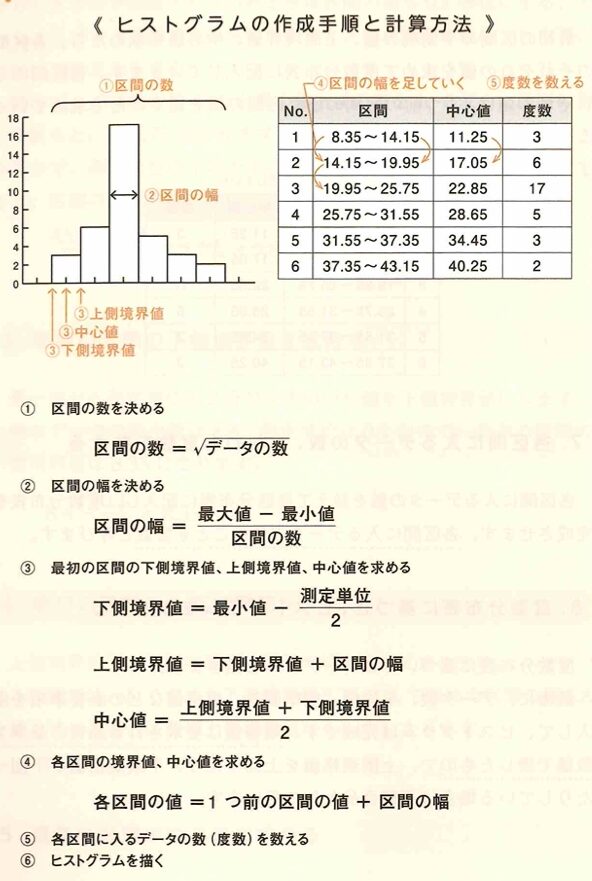
散布図
外れ値は原因がわかれば取り除きますが、原因不明の場合はそれを含めて散布図を見ます。ただし図FのようなQC検定特有の問題に注意しましょう。
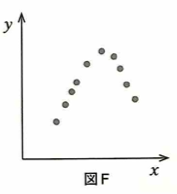
チェックシートは記録用チェックシートと点検用チェックシートがある
不適合項目調査用チェックシート→チェックを入れます。
不適合要因調査用チェックシート→データを層別します。
不適合位置調査用チェックシート→不適合が製品のどの位置にあるのかを調べます。
→不適合の要因を機械別などに層別。
度数分布調査用チェックシート→ばらつきがどのように分布しているか調査します。
点検用チェックシート→作業の流れに従いチェックマークを記入します。
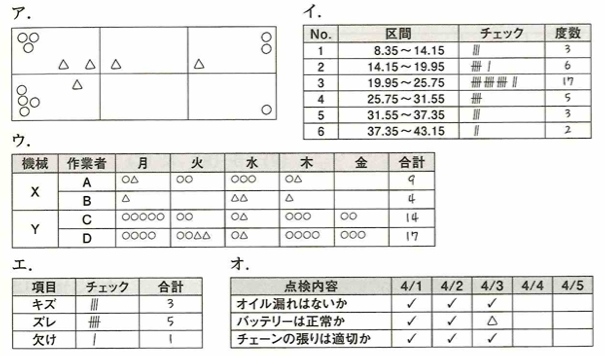
順に、不適合位置調査用チェックシート(不適合の発生場所の癖を知る)、不適合要因調査用チェックシート(寸法のばらつきがどのように分布しているか知る)、度数分布調査用チェックシート(どのような不適合がどれくらい発生しているか現象を知る)、不適合項目調査用チェクシート(不適合がどのような要因によって発生するか知る)、点検・確認用チェックシート(作業標準通りに製造が進められているかを管理)です。
グラフ・管理図
ガントチャート→活動の進捗を管理するのに適しています。カレンダーでも使われるもので実績を棒グラフで表します。
管理図
群とは工程からサンプリングしたデータの集合のことです。
QC検定3級で難易度の高い部分で次の3つを勉強します。
管理図の考え方と使い方
計量値→x̄-R管理図
計数値→p管理図(不適合品率の管理)とnp管理図(不適合品数の管理)
管理図は解析用管理図と管理用管理図の用途別に分けられます。
管理図は工程(インプットをアウトプットに変換する一連活動)の異常を見つけ、
安定状態(ばらつきが避けられない原因によってのみ発生している状態)を維持するために用います。
点が管理限界線の間にあり、点の並び方に癖(傾向)がない時に安定な状態と判断します。
管理限界線の外に点があっても工程が安定状態にないだけしか読み取れません。
x̄-R管理図
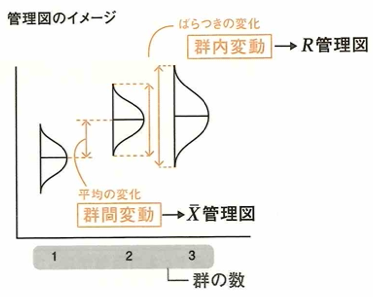
x̄は群間変動、Rは郡内変動を表します。
x̄-R管理図の書き方を教えてください!
一連の流れを図で解説します。
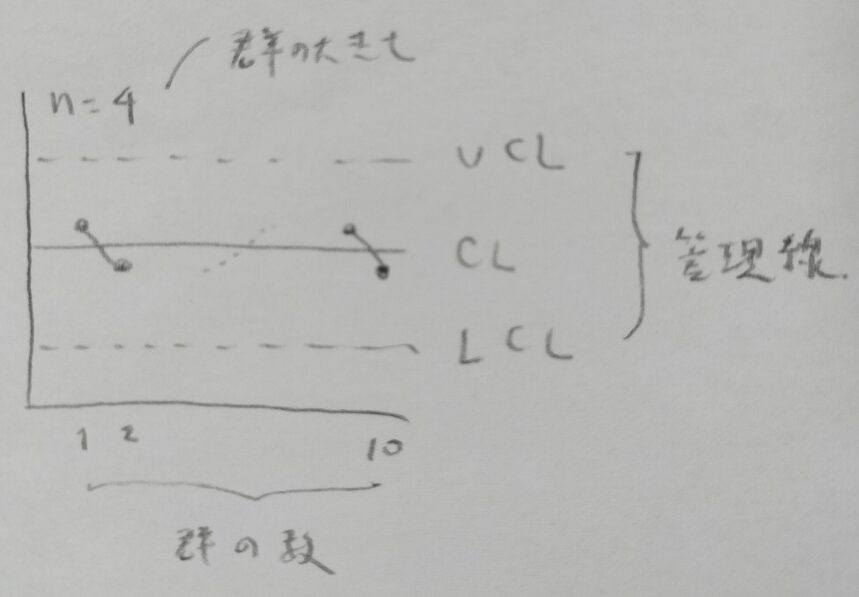
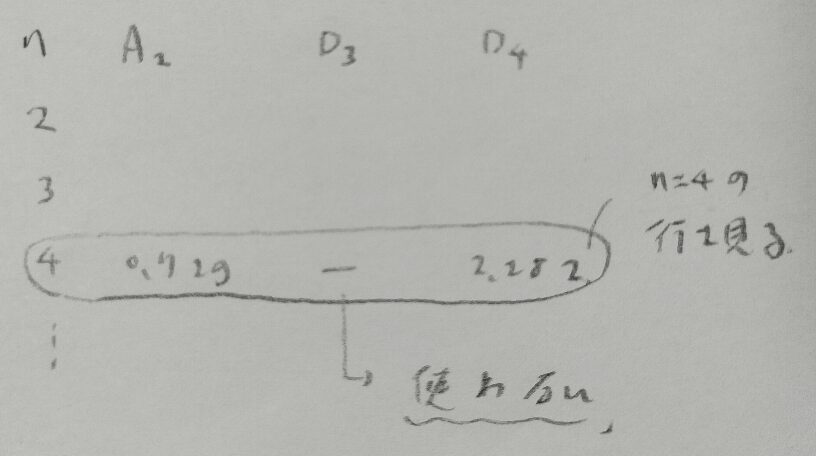
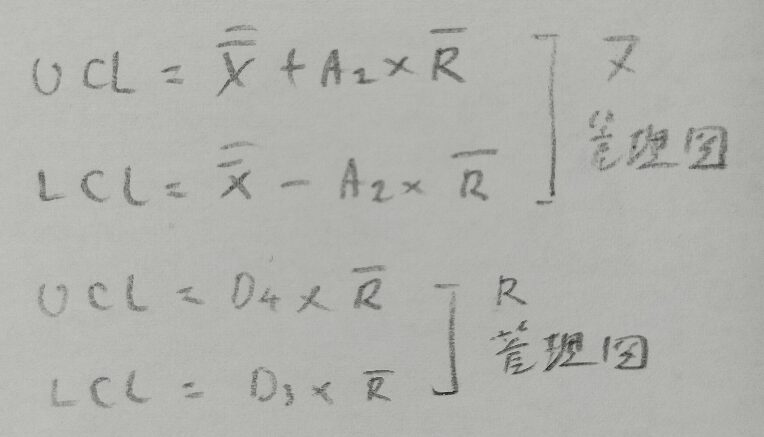
1:群の大きさnと群の数を確認します。
2:中心線CLを計算します。これは群の平均値x̄の平均値です。記号ではXの上にバーが2個つきます。
同様にR管理図ではCLを群の範囲Rの平均値で考えます。
3:管理限界線を計算するので係数表を用います。
4:CLから管理限界線に3σの距離で中心線からC,B,Aと区分けします。
これで工程が安定状態にある時は管理限界線の間に99.7%の点が入りますので、
工程が安定状態なのに外側に出てしまう確率が0.3%おきてしまいます。
慣れが必要なのは管理図の異常の判断です。
管理限界線を越える点の有無
長い連の有無
傾向の有無
周期の有無
中心線、管理限界線に接近している
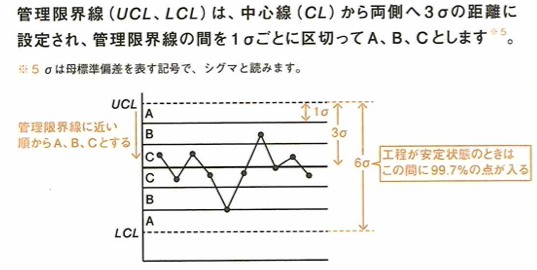
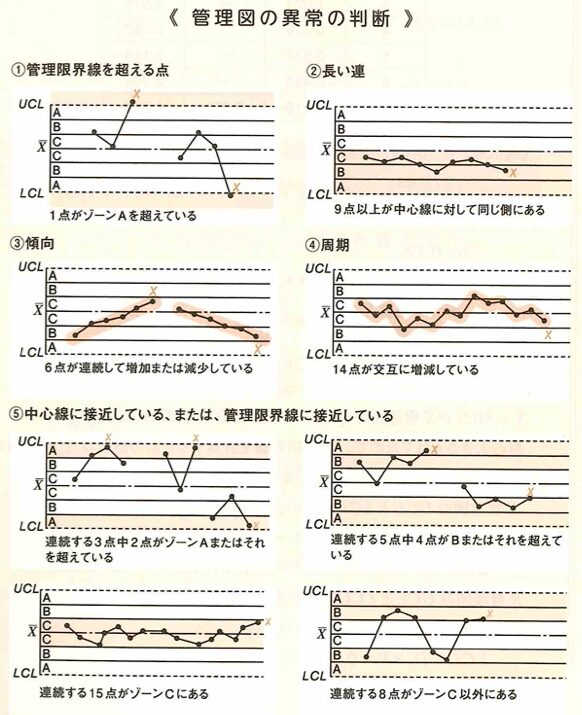
p管理図、np管理図
QC検定3級では細かいことは聞かれませんので黄色いマーカー部分をおさえておきましょう。
管理図 | 管理の対象 | 群の大きさ | 管理限界線の計算方法 |
p管理図 | 不適合品率 | 変動する | 各群に対し別々の管理限界線を計算。 群の大きさが小さいほど管理限界線の幅は広くなります。 |
np管理図 | 不適合品数 | 一定 | 全ての群で同じ管理限界線を用いることができます。 |
工程能力指数
工程能力指数とは安定状態にある工程が品質を実現する能力(工程能力)を測る指標です。データのばらつきがどれくらい余裕を持って規格内に収まるかを数値で表したものです。Cpで表し規格値(上限と下限があるものを両側規格で片側規格もあります)を用いて計算します。そのため管理図で安定状態であることを確認してから用います。
規格の中央に平均値がないときは、かたよりを考慮した工程能力指数Cpkを計算します。
結果は下記の計算で絶対値をつけたものになります。
一般にCpkの方がCpより悪い評価になります。
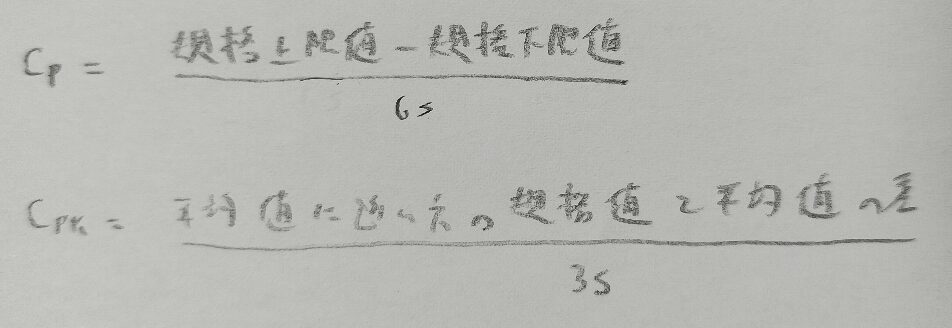
両側規格→Cp=(規格上限値ー規格下限値)/6s
→Cpk=(平均値に近い方の規格値と平均値の差)/3s
片側規格→Cp=(規格値と平均値の差)/3s
工程能力指数の値の基準はありますか?
1.33以上→工程能力は十分
1.00~1.33→工程能力はやや不足している
1.00未満→工程能力は不足している
ちなみに1.67以上で工程能力は十分すぎる。0.67未満で工程能力は非常に不足しています。
ヒストグラムを用いる際は余裕を持って規格内に収まっていればCpは十分。ギリギリでやや不足と判定します。
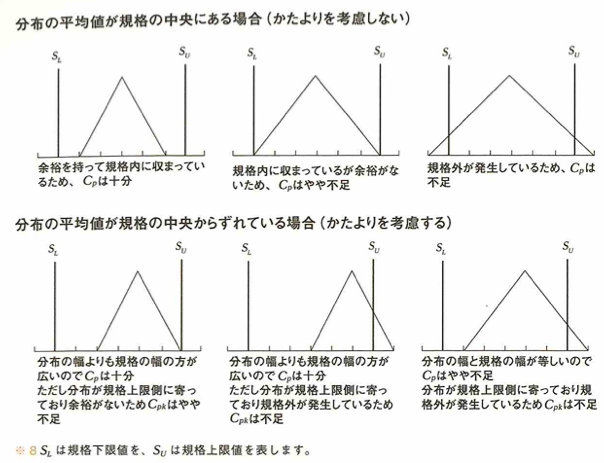
新QC七つ道具とは言語データを解析する手法です
語呂はパアママ親連携です。
QC検定3級から登場する内容です。定義と基本的な考え方を理解しましょう!
親和図法、関連図法、系統図法、マトリックス図法
アローダイアグラム法、PDPC法、マトリックスデータ解析法の7つです。
親和図法
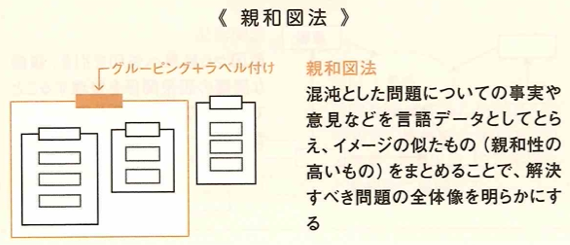
混沌とした問題を言語で表現し似たものをグルーピングします。
連関図法
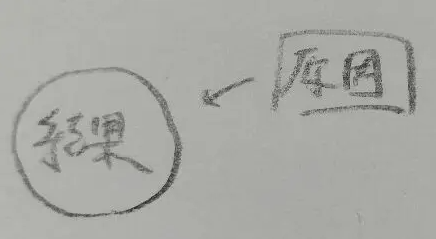
原因と結果が複雑に絡み合う問題の因果関係を論理的に矢印で繋いで整理します。
系統図法
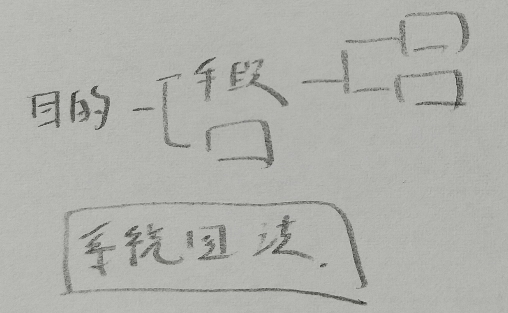
目的達成のための手段を系統的に展開し最適な手段を追求します。階層的もキーワードです。
目的→手段という流れが大切です。
目的を達成するための手段は?という流れですね。
マトリックス図法
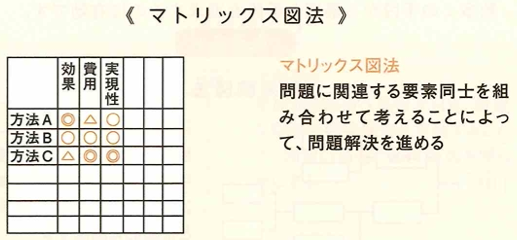
行と列の交点で要素同士の関係を示します。L字もキーワードです。
アローダイアグラム法
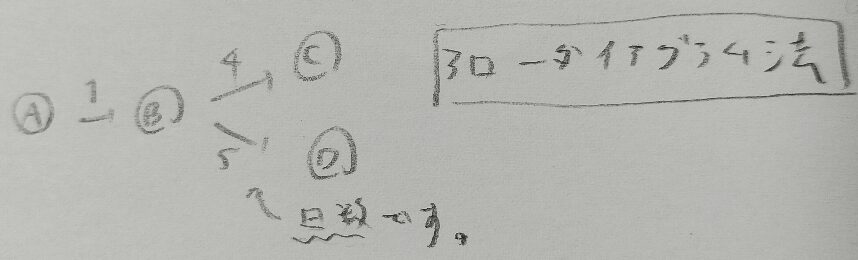
作業と日程の関連性を矢印で示し効率よく進捗管理(計画など)をします。
実はアローダイアグラムはITパスポートでも頻出事項です。対策はこちらです。
PDPC法
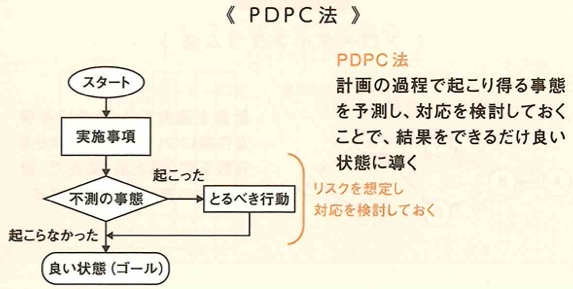
事前に問題を予測してリスクを回避して結果を良い方向に導きます。
プログラミングのような表記ですね!
アローダイアグラム法との違いはPDPC法は事前にリスクを予測する点です。
マトリックスデータ解析法(これだけ数値データを扱います)
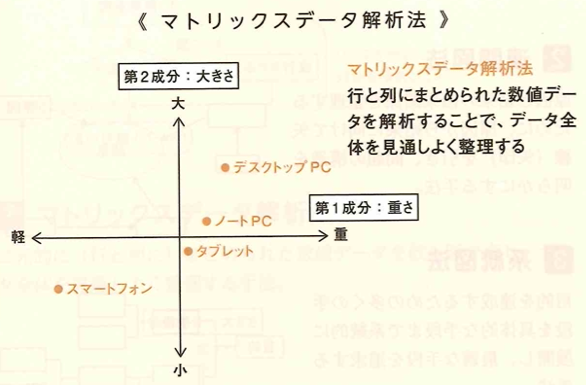
多くの数値データを二元的に見通しよく整理します。
マトリックスデータ解析法は新QC七つ道具ですが数値データを扱います。
QC検定3級の重要部分のインプットもこれで終了です!
QC検定4級の内容と合わせて学習したので効果的でした!
『ゼロからわかる! QC検定® 3級 テキスト & 問題集 新装版 [最新レベル表対応](TAC出版)』には各章に演習問題があり、最後には模擬試験もあるので対策はバッチリです。
QC検定3級の模試や過去問
QC検定3級:模擬試験
本書を用いたインプットが終わり少し経過した時点で巻末の模試を解きました。結果は83/103≒80.6%となり合格ラインを超えることができました。以下、模試を受けた後の注意点を書きます。
偏差平方和はxの2乗の合計ー((xの合計の2乗)をnで割った値)方が計算が速いです。
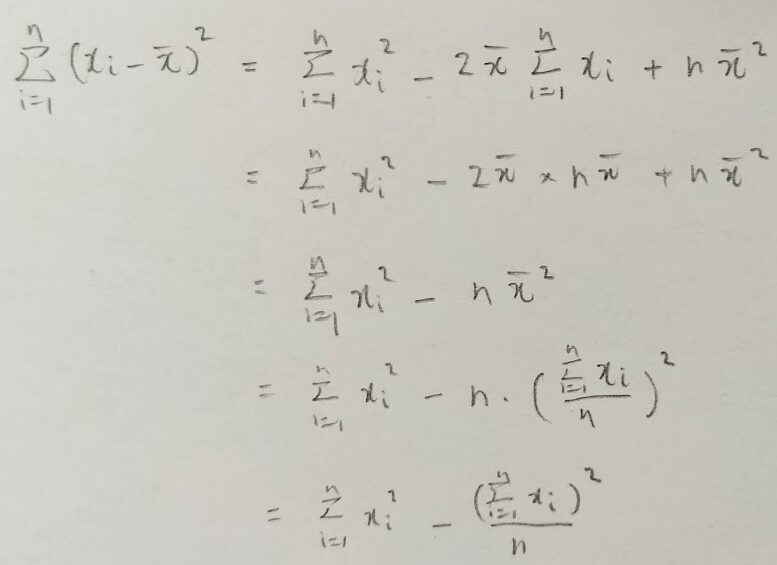
QC検定では標準偏差は統計検定でいうところの不偏分散の平方根に該当します。確率を求める問題で%単位が省略されていました。(この本だけかも知れません。)工程能力指数は、1.00≦Cp<1.33のときは工程能力はやや不足しています。1.00未満で不足しているとなります。工程能力指数=1とは、データの分布の幅と規格の幅が等しいことを意味します。1を下回ると規格外が発生していることになります。UCLとLCLの見間違いに注意しましょう。散布図では曲線的な相関がありそうという選択肢が答えになるときがあります。層別するという意味は広い意味です。問題があればQC工程図→作業手順書の順で調べます。工程における特性と要因の関係を明らかにするのは工程解析です。特性要因図などで考えていきます。DRはデザインレビュー、FTAは故障の木解析、FMEAは故障モード影響解析、品質保証体系図は、どの段階でどの部門が品質保証に関するどの活動を行うかを示した図です。品質特性は、品質要素を客観的に評価する指標です。回すのは管理のサイクルです。結果系の管理点(ゴロはかっけー)、要因系の点検点(ゴロは要点)が大事です。社内標準は実行可能で、遵守せねばならないという権威付けも大事です。QCサークル活動は継続的に行うボトムアップ型です。
次は手持ちの過去問を学習した記録になります。
QC検定3級過去問:第28回
第28回:72/100=72%(手法:34/50=68%、実践:38/50=76%)で手法編と実践編が足切りラインの50%を共に超え、全体でも合格ラインを超えましたがぎりぎりでした。早速復習します。
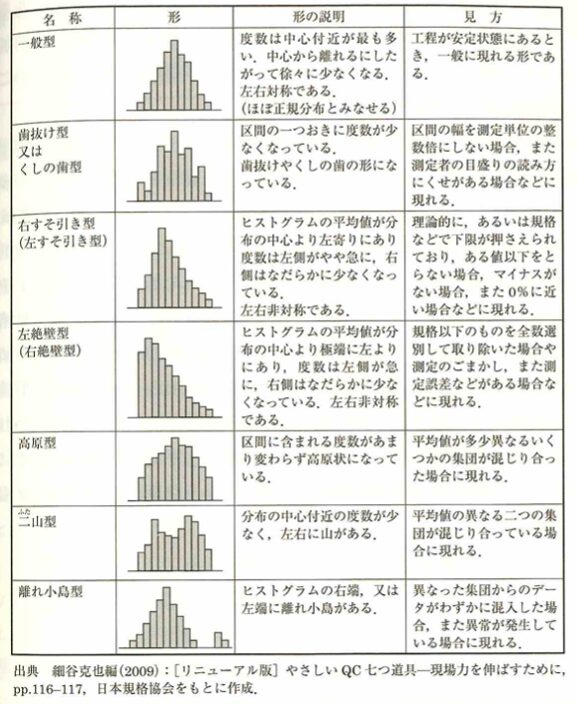
過去と現在を比較して変化や違いに着目して、原因を明確にしていくことが行われ、これを解析と言います。Cpの求め方の式の分子である上側規格ー下側規格の計算式ですが、それぞれ製品の規格として問題文に与えられていることに注意しましょう。5日間にわたって機械AとBの不適合項目別でその数を記録しているので、不適合調査用チェックシートです。さらに対象が不適合項目となっているので、不適合項目調査用チェックシートです。データ採取の際に手間をかけずに整理しやすくなるには事前にチェックシートを準備します。特性要因図は話し合いの道具とも言われます。パレート図の問題において何が問われているかに気をつけましょう。改善前の損失金額=改善前の不適合品数×1個当たりの損失金額です。改善効果なども問われていました。
こういった大問で問題の意図を読み落とすとかなりの問題数を失点してしまいます。気をつけましょう。
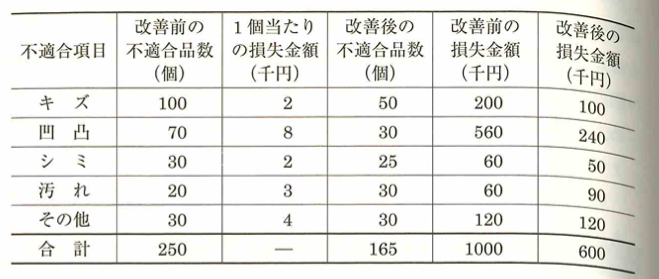
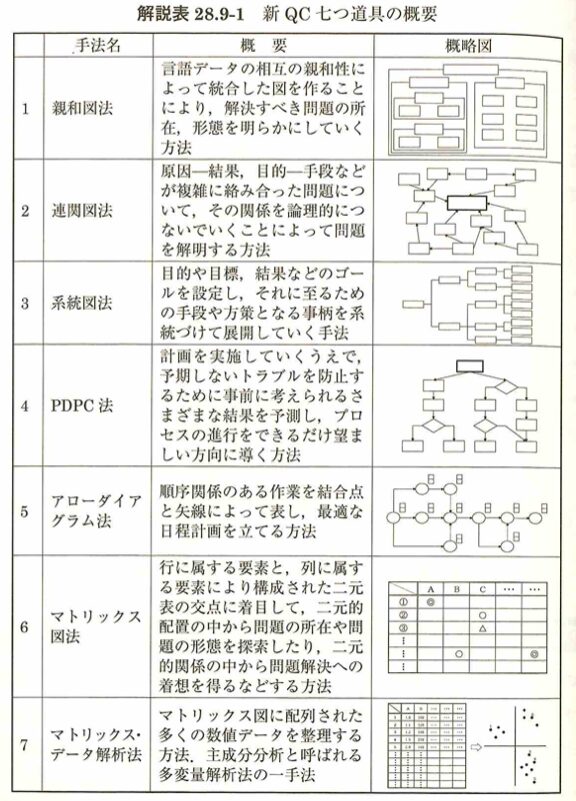
新QC7つ道具は似ている箇所が目立つので、上位級のことも考えて細部までしっかりと覚えておきたいです。
安定した良い工程から、安定した良いものができるとは、プロセス重視の考え方です。工程で異常が発生したら、応急処置→再発防止→未然防止まで対処します。製造の目標として狙う品質は、設計品質です。できばえの品質においてばらつきが生じます。製造で起きる品質は製造品質と呼ばれます。こらは適合の品質とも呼ばれます。それが満たされれば満足、不充足であれば不満を引き起こす品質を一元的品質と言います。充足でも不充足でも満足も不満も引き起こさない品質は無関心品質と言います。充足されると不満を引き起こし、不充足なら満足を与える品質を逆品質と言います。品質機能展開は、設計の意図を設計段階から製造段階まで展開することです。要求品質展開表と品質特性展開表の二元表は品質表と呼ばれます。FMEAは故障モード影響解析で、故障モードを洗い出し、発生度合いや影響度を評価します。設計段階において故障モードをもとに、製品使用時に発生する問題を洗い出す手法です。FTAは故障の木解析です。論理記号を用います。論理和と論理積があります。PLは製造物責任です。QC工程図はプロセスの流れに沿って管理すべきことを明確にしたものです。工程記号を使います。複合記号なども解説表に載っています。人が検査するときは、その力量を設定しておきます。狙った結果となるようにその原因となる工程の条件も点検しないといけません。出来栄えのチェックの対象を管理項目といい、工程の条件などを点検項目と言います。管理項目が管理水準を満たさない異常状態になる原因は、4Mの異常の他に、4Mの変化点があります。変化点が分かった時点でそのプロセスが引き続き安定した管理状態にあるか検討し、維持することが期待できない場合は異常発生時と同様に対処しないといけません。
QC検定3級過去問:第30回
第30回:90/98≒92%(手法:48/50=96%、実践:42/48≒88%)で手法編と実践編が足切りラインの50%を共に超え、全体でも合格ラインを超えることができました。第28回目の時と異なることは、第28回の過去問演習の後でこの記事の復習しただけです。ただし他の回でもこの得点率を取れるかはまだ分からないので、今後もしっかりと過去問演習に励みます。以下に復習なります。
p管理図は不適合率で工程を管理する管理図です。容器を群として管理すると、この問題では群の大きさが一定ではないので、群の大きさが一定でないとき割合を取って不適合率で管理するp管理図を用います。群の大きさが一定ならば不適合品数をそのまま使って管理できるのでnp管理図を用います。特性要因図は右端に解決したい問題を記入します。その問題となった結果(不具合内容など)を特性といいます。
応急処置は継続的なクレームには弱いが、是正処置は適します。是正処置が十分でないため引き続きクレームが発生していると考えられます。FMEAの実施に伴う評価の項目について、発生頻度の方が発生場所より評価の観点からは重要です。ガントチャートはステップ、担当、納期などを決められて1つの表にまとめることができます。
S:品質目標→標準化
D:標準について教育→標準通り実施
C:実施過程が標準通りか確認→実施結果と標準と比較
A:差異を原因を究明し処置→処置効果確認
標準化を行うことでノウハウが組織内に蓄積されます。
QC検定3級過去問:第31回
第31回:84/99≒85%(手法:44/50=88%、実践:40/49≒82%)で手法編と実践編が足切りラインの50%を共に超え、全体でも合格ラインを超えることができました。時間は75分かかり残り15分余るという割と苦戦した結果でした。過去問集は6回分の問題が掲載されており、多くの回の演習ができるありがたみを感じる結果となりました。
平均値を規格の中心に調整した場合、正規分布の平均値に関する対称性を用います。1点でも外れ値が回帰直線に乗る感じになると相関係数は高くなります。影響つまり結果とその要因の関係を可視化する方法は特性要因図です。真の原因を探すために要因分析を行います。寸法の中心とばらつきを知りたい時にはヒストグラムが適しています。どの設備のデータ化を考えるときは層別です。
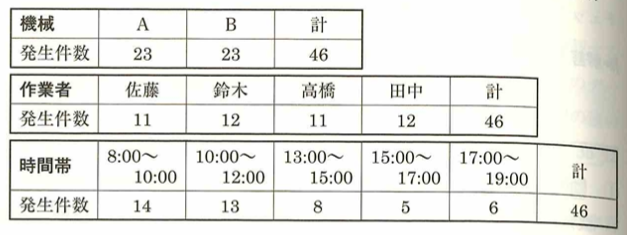
時には問題文から上のような感じで層別した不適合の発生件数を考えることも大事です。この時、不適合の発生件数に大きな違いが見られないのは、機械と作業者です。この問題が今回の第31回の中で最難問です。
品質保証体系図は、業務を各部門間に割り振ったものを体系的にまとめたものです。
製造品質はロットまたは工程の社内検査不適合品率やばらつきなどで表され、適合の品質とも言われます。図や写真を用いる作業などは作業標準です。文書であり作業の管理項目を対象とするのはQC工程図です。管理水準が明確になることにより通常か異常か判断できます。異常かどうか判定するための管理項目としての評価尺度が必要です。標準状態からの変更だが、アウトプットの製品に影響を与えないように変化した時点を変化点と言います。この変化点の管理が重要です。標準化による利益や利便が関係者間で公正に得られなければなりません。標準化は関係者で共通に使用できなかればなりません。
QC検定3級過去問:第32回
第32回:86/100=86%(手法:47/50=94%、実践:39/50=78%)で手法編と実践編が足切りラインの50%を共に超え、全体でも合格ラインを超えることができました。時間は76分かかり残り14分余るという実践編で粗を感じた結果でした。
管理図において、郡内ではできるだけ偶然変動によるばらつきのみが入るようにし、異常原因を含まないようにします。異常原因によるばらつきが、できるだけ群間の変動として現れるようにします。
特性要因図は、品質特性と要因の関係を明らかにしていくことから、工程管理に有効です。行に属する要素の対象と列に属する要素である評価項目との関係を表す数値データを解析することによって、評価項目を集約し、対象間や評価項目間の総合的な特徴を捉えるのに利用するのがマトリックス・データ解析です。
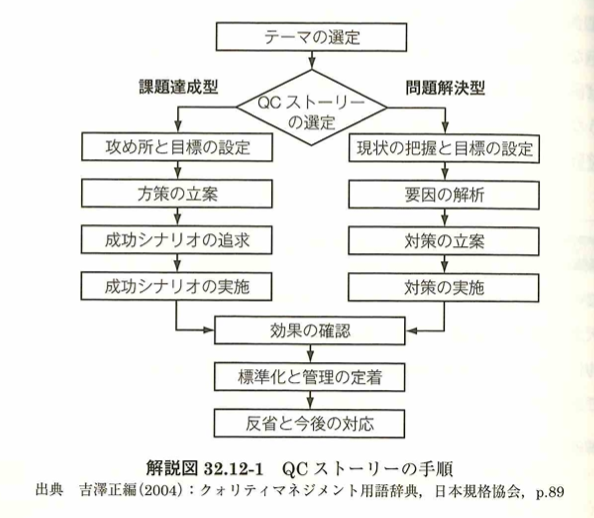
課題達成型QCストーリーは、成功シナリオの追求→成功シナリオの実施です。
起こったトラブルの再発防止に努め、起こる可能性のある気をつけていないトラブルを未然に防ぐ活動も大事です。
品質表(顧客と特性を合体)、QC工程表(標準化関連)、品質保証体系図(責任はどこにある?)はややこしいので次の説明で一気に覚えてしまいましょう!
品質保証体系図は、品質保証に関わる課・部門などの部署を横軸に、商品企画など一連の活動を縦軸に表示し、それぞれの活動に関わる部門、各活動の繋がりなどを一つの図にまとめたものです。QC工程図はプロセスの標準化を進めるツールです。記号を用いて流れを記述します。各工程の重要な品質特性に対する管理方式を5W1Hの視点から定めます。品質表=要求品質展開表+品質特性展開表です。
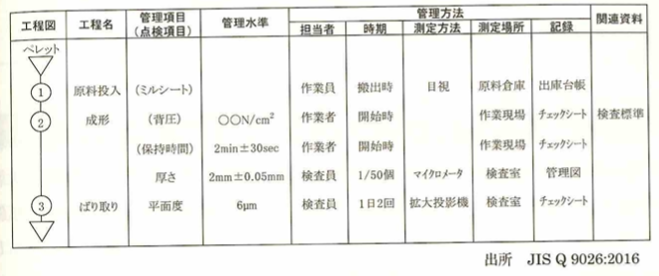
日常管理は現状を維持する活動が基本です。方針管理より経営資源を重点的に配分し経営のレベルアップを推進します。中長期計画や社内外の情勢や前年度の反省から方針を策定します。実行可能な実施計画書を作成して実施スケジュールを定めて方針を実施します。品質管理の教育を組織的に実施するため、階層別教育体系が整備されています。
QC検定3級過去問:第33回
第33回:89/102=87%(手法:47/50=94%、実践:42/52=87%)で手法編と実践編が足切りラインの50%を共に超え、全体でも合格ラインを超えることができました。試験が明日に迫りましたので、しっかりと気合を入れていきたいところです。
時間的順序で品質特性の観測値を打点した図を工程能力図と言います。
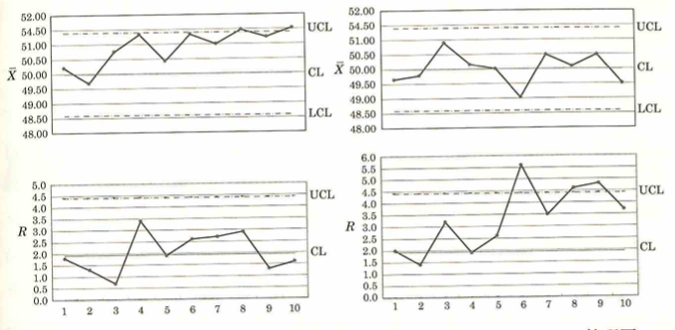
この時、aの上側から徐々に増えていき、下側から管理限界線に納まっていることがわかるので、工程平均が大きくなっています。bは上側は管理限界線に納まっており、下の図では管理限界線を超えるものが出てきていますので、Rは郡内変動を表すので、郡内変動が大きくなったと考えられます。
測定困難な時は代用特性です。顧客にとって充足されれば満足し、されなくても仕方ないと受け取られるのは魅力的品質です。プロセスの実態について事実を示すデータを把握します。・・・同じ原因で異常を発生させることがないよう恒久処置を行って再発防止を図る必要があります。経営方針により、(TQMにおいて)年度活動計画を立案・実施し、その結果をトップ診断で評価します。自らの組織の分掌業務を確実かつ効率的に達成するために必要な活動として、日常管理があります。これとQCサークル活動から得られた成果を、日常の業務で継続していくためには標準化を行います。・・・組織階層ごとにQC教育を実施することが重要です。標準化のねらいは、関係者が標準化の必要性を十分に理解し・・・標準化による効果は、関係する組織や人々に分配されるので・・・。
このような文章の問題はどの選択肢も合っているような気がしますが、正解は1つだけです。こうした問題に対しては公式が出している書籍を読むことが安全です。例えば、『【新レベル表対応版】QC検定受検テキスト3級 (品質管理検定集中講座[3])』です。本書まで取り組まなくても8割以上は得点できる感じですので、上位合格を狙う以外は購入する必要はないと考えています。
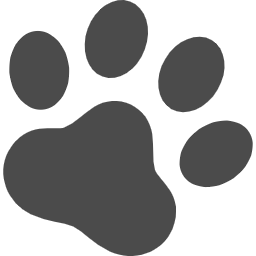
QC検定3級過去問:第34回
第34回:90/98=92%(手法:48/49=98%、実践:42/50=84%)で手法編と実践編が足切りラインの50%を共に超え、全体でも合格ラインを超えることができました。今までの自己ベストの点数となりました。ただしいつもよりも時間がかかりました。特にパレート図の問題で縦軸が%表記でないことに気づくのに時間を浪費してしまいました。それ以外でも実践の問題の難易度が高いと感じました。
系統図法は、問題に影響している要因間の関係を整理し、問題を解決するための手段を多段階に展開することによって最適手段を追求する場合に使用します。
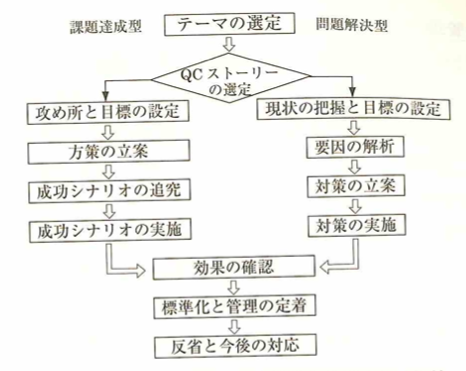
課題達成型QCストーリにおいて、方策の立案→成功シナリオの追求と実施です。SDCAサイクルは定められた標準に基づき業務を実施し、管理項目による確認を行い・・・できる限り定量化し、管理水準を設定する。製品の品質が安定している状態で、他の品質情報でロットを合否判断するのは無試験検査です。有効な手段としてアウトソース先に対する第二者監査を行うことがある。第三者は自社やアウトソース先のどちらにも利害関係のない組織のことです。
QC検定3級は改めて内容を俯瞰すると、広範囲の内容を扱う試験だということがわかりました。受験する方も共に頑張りましょう!
受験された方々もお疲れ様でした!QC検定2級の内容に進みましょう!